Nail making machines are essential in the modern manufacturing landscape, revolutionizing how nails are produced for numerous industries, from construction to DIY. These machines efficiently transform raw steel wire into nails through a streamlined process, involving wire cutting, head shaping, and tip sharpening. The evolution of nail making machines over time has led to enhanced accuracy, speed, and cost-effectiveness. With technological advancements, today’s machines are capable of producing uniform, high-quality nails on a mass scale, with precision that ensures every nail meets industry standards for consistency in size and shape.
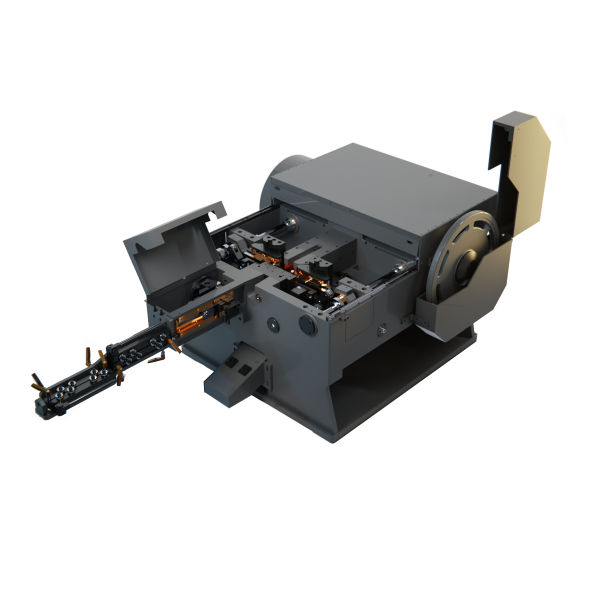
One of the hallmarks of modern nail making machines is automation, which reduces the need for manual intervention. These machines come equipped with features like automated wire feeders, precision cutting tools, and control panels that allow operators to monitor and adjust settings in real-time. This automation enhances production rates and minimizes human error, ensuring that the nails are consistently produced to the desired specifications. Additionally, these machines are versatile, designed to produce various types of nails, such as roofing nails, concrete nails, and nails for specific purposes across different sectors.
Materials used in nail manufacturing are crucial to the quality of the final product. Most nail making machines utilize high-grade steel wire, valued for its durability and resistance to corrosion. This steel must meet strict quality requirements, as impurities or inconsistencies can affect the nails’ performance and longevity. Many manufacturers work directly with suppliers to ensure high-quality raw materials that meet these standards. With the shift towards sustainable production, there is also an increasing interest in eco-friendly materials, which has started influencing the nail manufacturing industry’s choice of materials.
Nail Production Machine
The nail production machine is a comprehensive system that oversees every stage of nail manufacturing, from raw material input to final product output. Unlike single-function nail making machines, nail production machines are designed to handle multiple processes, including cutting, forming, and finishing, often all in one continuous sequence. These machines are instrumental in large-scale manufacturing operations that produce significant quantities of nails each day. By handling various stages of nail production automatically, nail production machines make high-volume, high-quality nail production a reality.
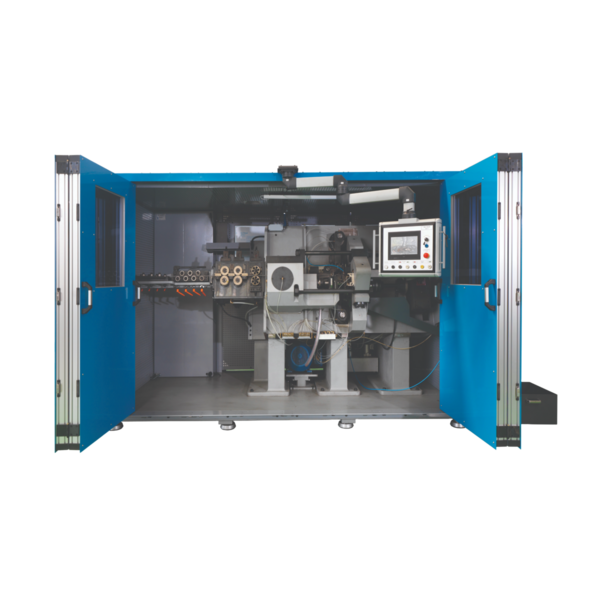
The production process starts by feeding steel wire into the machine, which is then cut to the required length. The machine shapes the head of the nail and sharpens the tip. For certain types of nails, additional steps, like threading or coating, may be necessary to meet specific application requirements. These fully automated systems ensure uniformity in the nails produced, with machines capable of adjusting for nail size, type, and purpose. This flexibility makes nail production machines suitable for producing a variety of nails, from common nails to specialized types used in construction or other industries.
The high-output nature of nail production machines makes them ideal for businesses that need to produce nails on a large scale without compromising quality. With speeds capable of producing thousands of nails per minute, these machines ensure that manufacturers can meet even the most demanding production requirements. Many machines come equipped with automated quality inspection systems that monitor each nail as it’s produced, ensuring that any nails that don’t meet quality standards are automatically rejected, further maintaining high standards throughout the production line.
Regular maintenance and operator training are essential to keep nail production machines functioning efficiently. Due to the complex nature of these machines, operators must be familiar with their setup, operation, and maintenance requirements. Routine maintenance includes tasks such as lubrication, part replacement, and calibration, which help avoid costly downtime and ensure long-term machine performance. Manufacturers often provide detailed guidelines and schedules to assist operators in maintaining optimal machine performance, making these machines a smart investment for high-capacity production facilities.
Nail Manufacturing Machine
The nail manufacturing machine is the backbone of nail production operations, designed to handle everything from raw material processing to finished nail output. These machines are often part of an integrated production line, working alongside wire drawing and coating systems. Their versatility makes them suitable for producing a range of nail types, including but not limited to roofing, masonry, and finishing nails. This comprehensive approach to nail production streamlines the entire process, making it easier for manufacturers to produce consistent, high-quality nails for various uses.
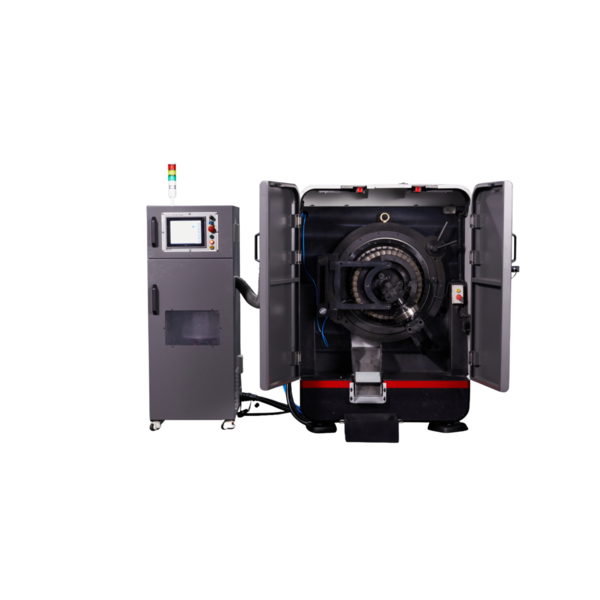
The nail manufacturing process involves multiple stages. First, the steel wire is drawn to the desired thickness, then fed into the machine, where it is cut and shaped into nails. Depending on the nail type, the machine may also add threads or apply a protective coating, such as galvanizing for corrosion resistance. This careful process ensures that each nail meets the required specifications in terms of size, shape, and durability. Advanced machines allow for a high level of customization, making it possible to adjust the machine for different nail types and sizes with minimal downtime.
Technological advances in nail manufacturing machines have improved efficiency and precision. Many machines now feature CNC systems that provide operators with a high degree of control over production variables. These systems allow for greater consistency across production batches, which is essential for meeting industry standards. In addition, automated inspection systems use sensors and cameras to check each nail for defects, ensuring only the highest-quality nails are packaged and shipped. This level of quality control is invaluable in industries where even minor defects can impact the product’s performance.
Maintenance is key to maximizing the performance and lifespan of nail manufacturing machines. Due to their high-speed operations, these machines are subject to significant wear and tear. Regular maintenance tasks include lubricating moving parts, replacing worn components, and ensuring proper calibration. Manufacturers often provide maintenance schedules to guide operators, helping to prevent breakdowns and extend the machine’s useful life. Proper maintenance not only keeps the machines running smoothly but also helps manufacturers maintain a steady supply of nails to meet demand.
Thread Rollers
Thread rollers are specialized machines used in nail and fastener manufacturing to create threads along the shank of nails and screws. This threading process is crucial for nails that need extra holding power, such as those used in structural or heavy-duty applications. The thread rolling process involves pressing the nail between two dies, which deform the shank to create threads without removing any material. This process strengthens the nail and produces a thread with smooth, precise contours, making it highly effective for applications that require superior grip.
Thread rolling offers several advantages over traditional cutting methods for creating threads. For one, the rolling process is faster and more efficient, making it ideal for high-volume production lines. Second, because the process compresses the material rather than removing it, thread-rolled nails are often stronger and more durable. Third, rolled threads have a smoother surface finish, which enhances the nail’s performance and makes it easier to drive into materials. These qualities make thread rolling an ideal method for producing high-quality threaded nails and fasteners.
Modern thread rollers are designed with advanced control systems that allow operators to adjust the thread pitch, depth, and shape according to the specifications required. These machines are often used alongside other production equipment, making it easy for manufacturers to switch between different types of nails or screws with minimal setup time. Thread rollers also typically come with quality control systems that ensure each nail’s threads are uniform and free from defects, contributing to the overall quality and reliability of the product.
Maintaining thread rollers is essential for consistent production quality. Regular maintenance includes replacing worn dies, lubricating the machine, and ensuring the feed mechanism is properly aligned. Preventive maintenance helps to avoid unscheduled downtime and keeps the machine performing at optimal levels. Training operators on maintenance and best practices ensures that thread rollers remain efficient, producing high-quality threaded nails and screws that meet market demands.